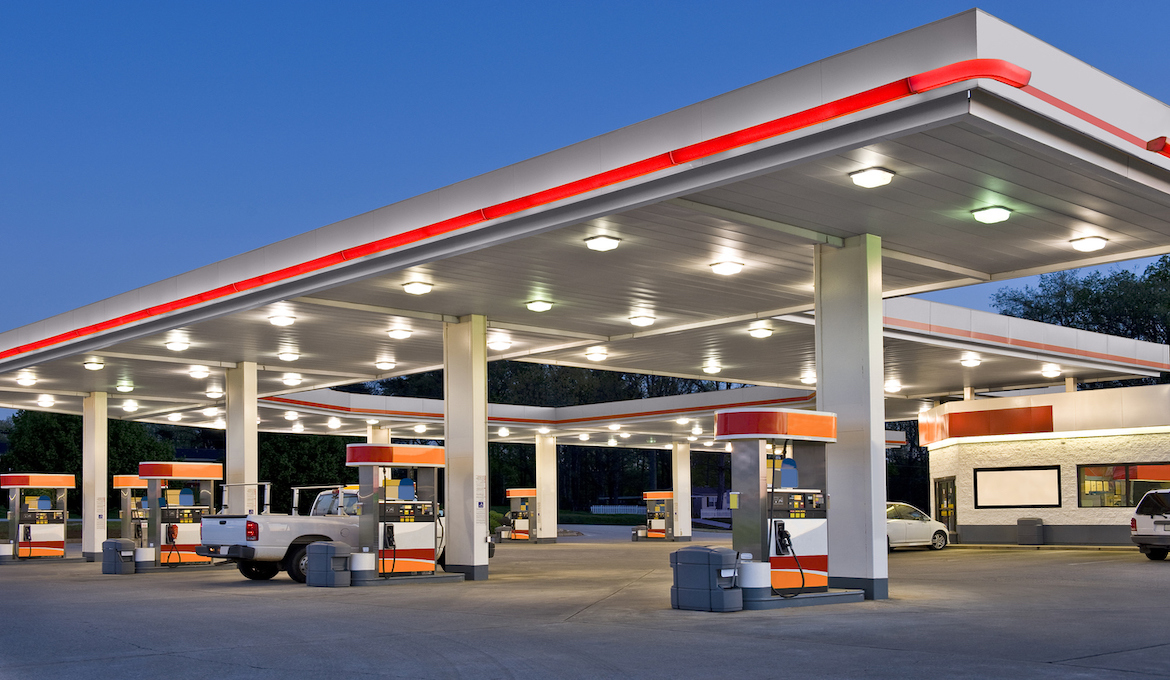
Webinar Recap: Fuel Inventory Variance Control – Why Speed and Precision Matter
In the third and final session of our Future of Filling Up: Faster, Easier, Frictionless webinar series, Titan Cloud’s Vice President of Solutions Consulting Paul Lauinger and TRUEFILL Co-Founder & President Wade Lowe explored the ways connectivity, visibility and automation can optimize fuel logistics, assets and operations.
Here are some takeaways from the conversation. To catch a full recording of the webinar, From Chaos to Clarity: Demystifying Fuel Logistics visit here.
In response to one of the webinar’s poll questions, more than half of the attendees reported experiencing higher operating costs due to reactive or over-allocation situations. The conversation turned to visibility into those allocations, and how differing workflows can impact the flow of information.
“Although it would seem that most companies’ workflows would be the same—because they’re doing the same job for all intents and purposes—it’s actually not true. About 80% of a workflow may be the same as another, but 20% is different,” said Lowe. “And it’s not always different in the same way; it’s different in a unique way, every time. Even if an operator’s workflow is, I need to buy, move, deliver, and reconcile, how they operate is unique inside each business. Exceptions and errors happen because in any fuel transaction, so many manual components are operating across multiple systems, groups, and individuals. It can create a lot of havoc.”
To reduce the large number of touchpoints inherent in traditional fuel transactions and lessen the opportunity for error, Lauinger and Lowe outlined the critical role of automation.
“You’ve got your supply team determining best buy, operations team responsible for executing on that strategy to get the fuel where it needs to go, and the back office. Those three different components inside of a business typically work in siloes and you have to use different systems for each one,” Lowe explained. “When you automate, you centralize all of that so your supply team, your operations team and your back-office team are all in one place; you don’t have disparate systems and different people in different places trying to figure out what’s going on.”
Lowe was also quick to add that integrating automated technology into the fuel supply chain doesn’t replace employees, it enhances their productivity.
“We’re not suggesting that people don’t need to be involved. What we are suggesting is that technology can help people make better decisions,” he said. “If we’re looking at the fuel inventory levels and the consumption rates, the system can predict what needs to go, as well as the where, when and how, and it will build loads. That allows the dispatcher to focus on dispatching, not on figuring out what sites are about to run out or not. The system’s handling that.”
Lowe and Lauinger agreed that fuel supply chain technology and automation should be viewed as a co-pilot charged with reducing manual touchpoints, minimizing errors, and streamlining operations. Fuel operators who integrate such platforms will gain the centralized visibility needed to optimize operations and drive revenue.
To watch a recording of the full conversation, From Chaos to Clarity: Demystifying Fuel Logistics, visit here.