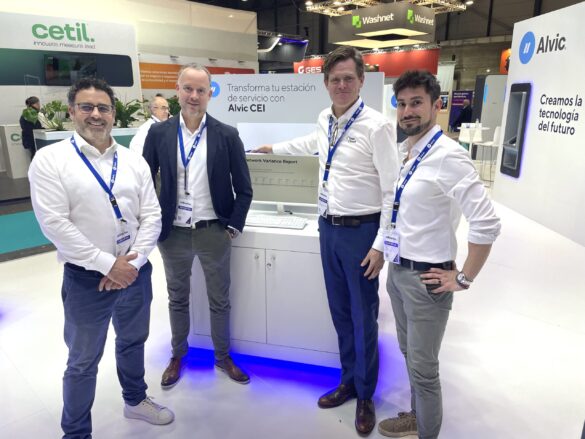
Motortec Madrid 2025: Alvic & Titan Cloud on Accessing the Full Benefits of SIR
This article originally appeared in forecourttech, July 2025
At recent industry tradeshows that took place around Europe, I had the opportunity to connect with fuel retailers looking for ways to digitalize the management of service stations, distribution centers, and vehicle fleets.
Many of those discussions revolved around Statistical Inventory Reconciliation (SIR), and we’ve noticed that SIR can sometimes still be perceived as compliance checkbox. However, there is much more to it: Beyond the obligatory nature of SIR lies a far greater opportunity.
By transforming raw data into actionable insights, SIR helps reduce fuel losses, optimize maintenance, increase profitability, and safeguard your business from operational and financial risks, making it a strategic tool for fuel analytics.
Real-time data around leak detection or inventory variance enables a wetstock manager to act quickly, addressing issues before they negatively impact site operations or customer experience, or before they trigger violations and fines. By centralising and analysing key existing data, SIR can provide a valuable business advantage offering efficiency, cost reduction and regulatory compliance.
In Spain, for example, as in other European countries, SIR is either required by law or highly encouraged as best practice. In this market, we have partnered with Alvic Group to offer Alvic CEI SIR, which uses Titan Cloud technology to collect and monitor systems data at retail fuel sites to support precision wetstock management control. At the same time, the volume and quality of the data being collected provides a body of critical and actionable insights that can be used to optimize operations.
Many fuel operators today are focusing on ROI—whether for mid-market retailers optimizing every euro or enterprise organisations looking to expand in the region.
Here, too, the ability to have multiple data streams fed into a single source of truth, provides a significant business advantage. SIR can help fuel retailers identify issues such as tank or line leaks, inaccurate tank gauging, water ingress, unrecorded sales, over-dispensing meters, theft, delivery shortfalls and more.
All in all, SIR is the right solution for fuel retail networks who are not only focused on reducing compliance costs but are also committed to optimizing their overall operations. This includes minimizing fuel loss across the system and improving alarm management by significantly reducing false alarms. It’s a solution for network operators who see operational excellence as a strategic business advantage.
To fully realise the benefits of SIR and wetstock management, fuel retailers must first overcome a critical challenge: Collection of data from their sites.
Working with those in the industry to collect that data at the lowest possible cost and with minimal disruption, we focus on two main fronts: First, ensuring that the Titan Cloud platform can connect to all major forecourt control systems (such as DOMS and Alvic), and second, helping to define global industry standards that enable the entire ecosystem to benefit from this data. Key industry organisations like IFSF (Europe) and Conexxus (US) are actively involved in advancing this topic. They’ve developed comprehensive data dictionaries that define and standardise key concepts, data elements, and business terms across the forecourt and retail fuel industries. These dictionaries are widely used by stakeholders to ensure consistency in integration, reporting, and system interoperability.
The absence of standardization across different countries can make wetstock management projects more expensive and technically challenging, limiting growth opportunities. Standardization, on the other hand, can unlock operational efficiency, data intelligence, and scalable growth across borders.
Want to learn more? Let’s connect at Forecourttech 2025, 1-2 October, Spain, where I’ll be taking part on the session ‘The Debate on Data Connectivity and Data Security’.
Get in touch with us to schedule some 1:1 time on-site!